Hydraulic cylinder processing
A hydraulic cylinder is a mechanical actuator used to provide linear movement and force by using pressurized hydraulic fluid. It consists of a cylindrical barrel, a piston connected to a rod, and seals and ports to control the flow of fluid.
The hydraulic cylinder works by converting the energy of pressurized fluid into linear motion and force. The fluid is pressurized by a pump, and then directed into the cylinder, pushing the piston and extending the rod. Reversing the flow of fluid retracts the piston and rod.
Hydraulic cylinders are commonly used in industrial and mobile applications where linear movement and force are required, such as construction equipment, material handling, and manufacturing processes. They offer advantages such as high force output, quick response time, and precise control, making them a popular choice for a wide range of applications.
Hydraulic cylinders come in various shapes, sizes, and capacities, and can be customized for specific applications. The choice of hydraulic cylinder will depend on factors such as the required force, speed, and stroke length, as well as environmental and operational conditions.
Hydraulic cylinder Specifications:
Hydraulic cylinder specifications refer to the various dimensional, functional, and performance characteristics of hydraulic cylinders. The following are some of the common specifications for hydraulic cylinders:
- Bore size: The diameter of the piston, which determines the maximum fluid volume that can be contained in the cylinder.
- Stroke length: The maximum linear distance that the piston rod can travel from the fully retracted position to the fully extended position.
- Rod diameter: The diameter of the piston rod, which determines the amount of force that can be applied to the load.
- Retraction speed: The time required for the piston rod to travel from the fully extended position to the fully retracted position.
- Extension speed: The time required for the piston rod to travel from the fully retracted position to the fully extended position.
- Operating pressure: The maximum operating pressure of the hydraulic fluid, which determines the maximum force that can be generated by the cylinder.
- Sealing: The type and quality of seals used to prevent fluid leakage and protect the cylinder from external contaminants.
- Mounting options: The various mounting options available for the cylinder, such as flange, clevis, and trunnion mounts.
- Material: The materials used for the cylinder barrel, piston rod, and seals, which determine the strength, durability, and resistance to corrosion of the cylinder.
- Temperature range: The operating temperature range of the hydraulic fluid, which affects the performance and lifespan of the cylinder.
These specifications can vary widely based on the type and intended use of the hydraulic cylinder, and should be carefully considered when selecting a hydraulic cylinder for a specific application.
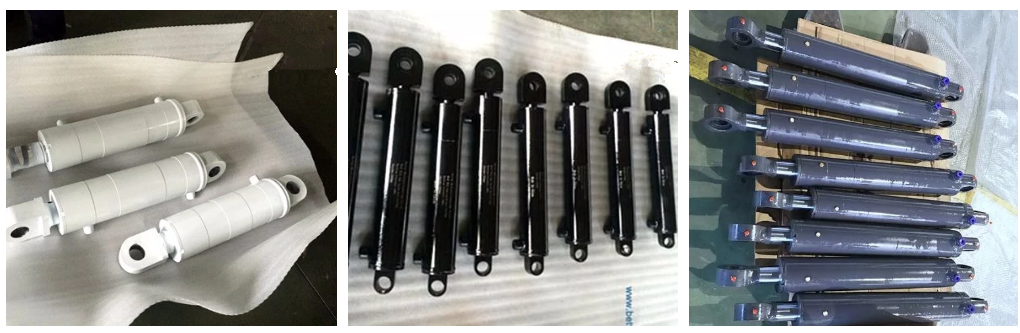
Hydraulic cylinder processing:
Hydraulic cylinder processing refers to the various operations performed on hydraulic cylinder components during the manufacturing process. This includes machining, welding, heat treatment, surface finishing, and assembly.
- Machining: This involves cutting and shaping the metal components to their desired dimensions and features using specialized machines and tools, such as CNC (computer numerical control) machines, lathes, and mills.
- Welding: This involves joining the components of the hydraulic cylinder together using welding techniques, such as MIG (metal Inert Gas) welding or TIG (Tungsten Inert Gas) welding.
- Heat treatment: This involves subjecting the metal components to controlled heating and cooling processes to improve their mechanical properties and ensure consistent quality.
- Surface finishing: This involves applying a protective coating to the components to improve their corrosion resistance and enhance their appearance. Common surface finishes include electroplating, painting, and powder coating.
- Assembly: This involves putting together all the machined components to form the complete hydraulic cylinder, including installing the seals, ports, and any other necessary components.
The hydraulic cylinder processing is typically performed by experienced professionals using specialized equipment and techniques to ensure high quality and consistency. The various processing operations must be carefully controlled to meet the design specifications, industry standards, and performance requirements of the hydraulic cylinder.
Hydraulic cylinder machining :
Hydraulic cylinder machining refers to the process of manufacturing hydraulic cylinders by cutting and shaping metal materials to create the various components of the cylinder. This includes machining the cylinder barrel, the piston, the rod, and the end caps.
The hydraulic cylinder machining process typically involves several steps:
- Raw material preparation: The raw materials, such as steel or aluminum, are cut to the correct lengths and prepared for machining.
- Cylinder barrel machining: The cylinder barrel is machined to the correct diameter and length, and the ports for fluid inlet and outlet are drilled.
- Piston machining: The piston is machined to the correct size and shape, and the seals and ports are added.
- Rod machining: The rod is machined to the correct diameter and length, and the threads and other features are added as needed.
- End cap machining: The end caps are machined to the correct size and shape, and the mounting options are added.
- Assembly: The machined components are assembled to form the complete hydraulic cylinder.
- Testing: The hydraulic cylinder is tested for proper operation and leak-free performance.
Hydraulic cylinder machining requires specialized equipment and expertise to ensure precision and accuracy, as well as adherence to strict quality and safety standards. The machining process is typically performed by experienced professionals using CNC (computer numerical control) machines, which are programmed to produce the components to precise specifications.